Linkwin has implemented a large number of smart manufacturing system integration projects combining informatization and automation. We provide customized solutions including production line automation transformation, product digital traceability, production process monitoring, and warehouse logistics management.
Through Smart Line and Smart Workshop solutions, WinIoT gives full play to the advantages of automation, informatization, digitization and intelligence to improve efficiency and reduce costs for manufacturing.
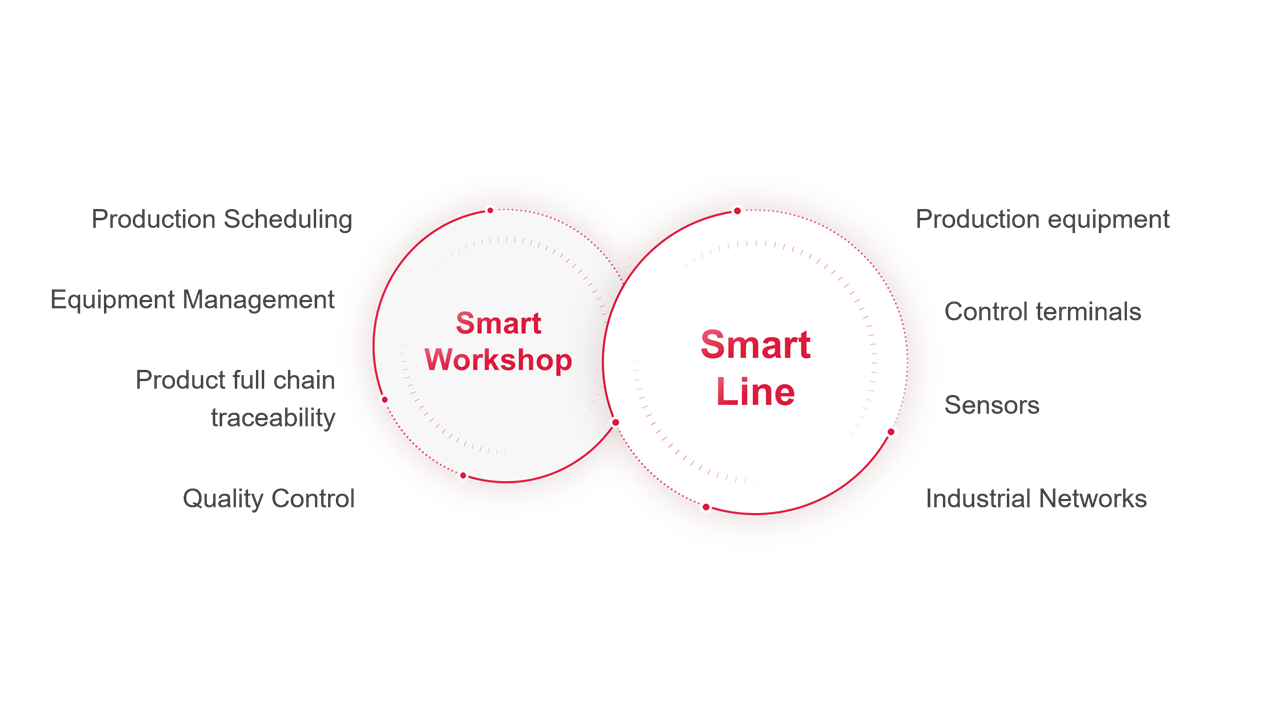
-
01Flexible multiple acquisition methods
Real-time grasp of production line equipment operation, so that managers can view the factory equipment production status without leaving their desks.
-
02Tracking and analysis of production process and equipment status
Record and track the time spent by each operator of each machine, helping factory managers to truly grasp the utilization of resources and to make improvements in the production process, thus reducing unnecessary waste.
-
03Analysis of the actual production capacity of lean manufacturing
Assist companies to easily identify bottlenecks affecting productivity, improve and track them, and improve efficiency.
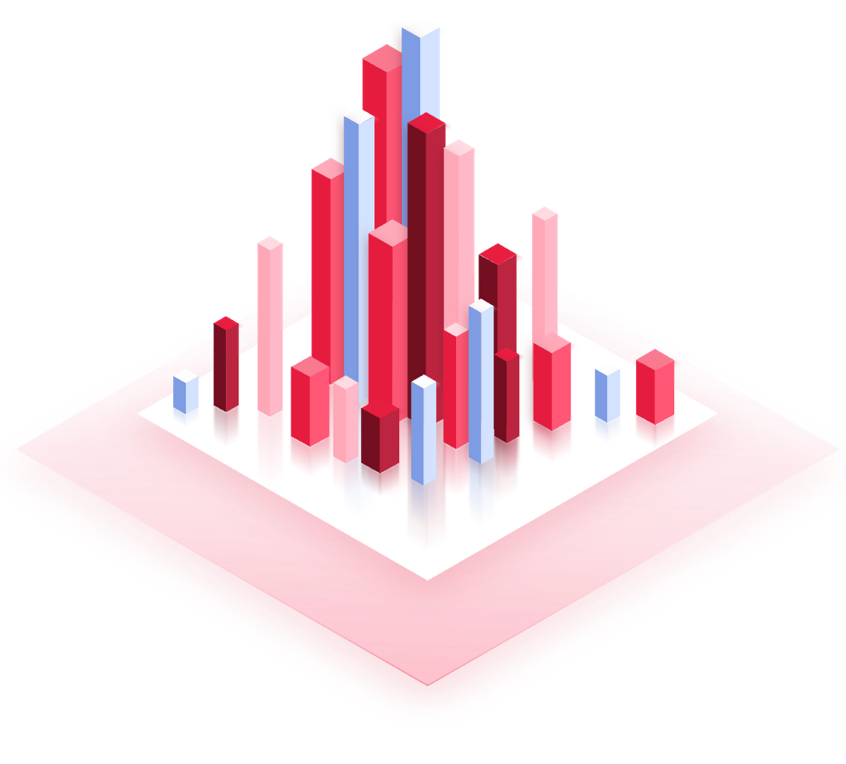
-
04Flexible combinations of Kanban management
Significantly improve the information transparency and production process controllability, helping companies to understand the situation and make timely decisions.
-
05Performance and productivity assessment
Help managers to effectively manage their employees through performance ranking analysis and create a positive competitive atmosphere for their production sites.
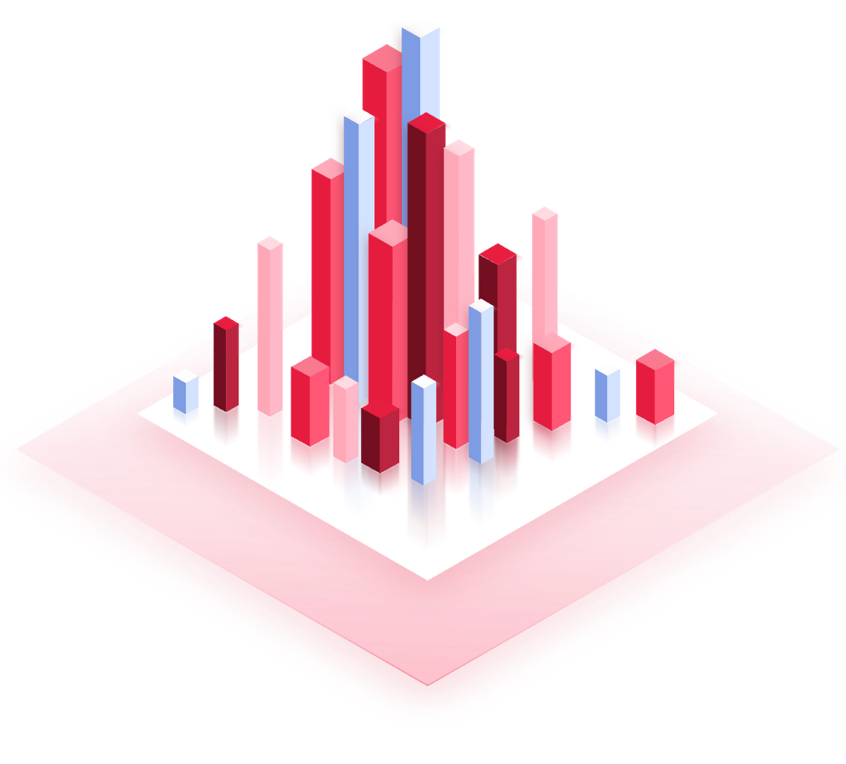
-
01Flexible multiple acquisition methods
Real-time grasp of production line equipment operation, so that managers can view the factory equipment production status without leaving their desks.
-
02Tracking and analysis of production process and equipment status
Record and track the time spent by each operator of each machine, helping factory managers to truly grasp the utilization of resources and to make improvements in the production process, thus reducing unnecessary waste.
-
03Analysis of the actual production capacity of lean manufacturing
Assist companies to easily identify bottlenecks affecting productivity, improve and track them, and improve efficiency.
-
04Flexible combinations of Kanban management
Significantly improve the information transparency and production process controllability, helping companies to understand the situation and make timely decisions.
-
05Performance and productivity assessment
Help managers to effectively manage their employees through performance ranking analysis and create a positive competitive atmosphere for their production sites.
WinIoT platform is located in the middle core layer of IoT technology, and its main role is to connect intelligent devices downward and undertake application layer upward.
Rooted in PaaS environment, WinIoT platform grows with data as nutrients and empowers data to downstream applications through various types of platform processing, presenting the logic of gradual ascension of data value from upstream terminals to downstream users. In the era of Internet of Everything, data value ascension is generated by the demand of unified management of IoT devices across businesses, and its key components are four types of platforms.
1) Connection management platform: to solve the access of massive heterogeneous devices across business stacks.
2) Device management platform: unified management, control and firmware upgrade of devices.
3) Application enablement platform: providing data development tools and environment.
4) Business analysis platform: access to cloud computing and AI and other data analysis capabilities to provide data insight services for customers.
-
Unified Data StandardsWe build a standardized data platform for enterprises by constructing standards for data access, storage and usage by means of object model & business model.
-
Unified Integration StandardsThe integration tools can quickly integrate applications & data, greatly reduce integration costs, realize the interface between systems with a unified architecture and standards, and establish standards and accumulate results for enterprise system integration.
-
Unified Application StandardsThrough the platform's industrial application configuration and development tools to build a unified platform application development and access standards, to achieve the standardization of platform applications and solve the problem of enterprise application silos.
-
Unified User StandardsAll applications of the platform use a unified user system, and one account can use all the platform applications.
Connect manufacturing equipment to achieve equipment data collection, status monitoring, OEE analysis, etc.
-
Productivity Management
Process monitoring
Enables complete line monitoring from the refining process to the final product packaging.
Close monitoring identifies production lags and eliminates waste and unnecessary product inventory.
QR System:
Real-time data collection on the production line through QR code scanning data different from each single product coupled with WinHUB to achieve OEE of production line performance and personnel performance assessment.
-
Equipment Management
Equipment health management
Historical data and machine learning technology can establish equipment fault prediction model to realize fault diagnosis and predictive alarm for high-value equipment and key components, and reduce the number of reactive maintenance or preventive maintenance.
Remote maintenance
Real-time online data, remote monitoring, group control debugging, parameter adjustment, and control execution are available.
-
Energy Management
Energy consumption analysis
Based on the energy consumption analysis of historical data by machine learning, it calculates the optimal energy consumption under average working conditions, supplemented by real-time evaluation of energy consumption status, energy consumption risk warning and energy consumption trend prediction.
Parallel dispatch abatement
In multi-plant, multi-process and multi-equipment situations, it extracts production and emission-related operation data in real time for mining, prediction and early warning, and calculates energy consumption in advance to achieve dynamic optimization of cross-process energy efficiency.
-
Security Monitoring
Safety and security
Improve the overall safety and security of plant employees. By monitoring health and safety KPIs such as injury and illness rates, attempted incidents, occasional and chronic absenteeism, vehicle accidents, and property damage or loss in daily operations, effective monitoring ensures better safety and lagging indicators, if any, can be addressed to ensure health, safety and environmental (HSE) issues are properly remediated.