Introduction:
Over the past 20 years since its establishment, LINKWIN has worked hand in hand with many Fortune 500 companies to jointly explore the boundless possibilities of digital transformation. LINKWIN will regularly share a series of cases, including the overview of cooperative enterprises, solution overviews, project application values, industry insights, and predictions.
Cooperative Enterprise Overview
This enterprise is a subsidiary of a globally leading energy group, specializing in providing high-quality lubricants and related services to both consumer and industrial customers. It offers comprehensive lubrication solutions across various sectors such as automotive, industrial, aviation, and marine, with a product line that encompasses engine oils, transmission oils, hydraulic oils, industrial lubricants, and many other types.
With its high-quality products, innovative technologies, and exceptional services, this company holds a prominent position in China's lubricant market and is widely recognized as one of the industry leaders.
Solution Overview
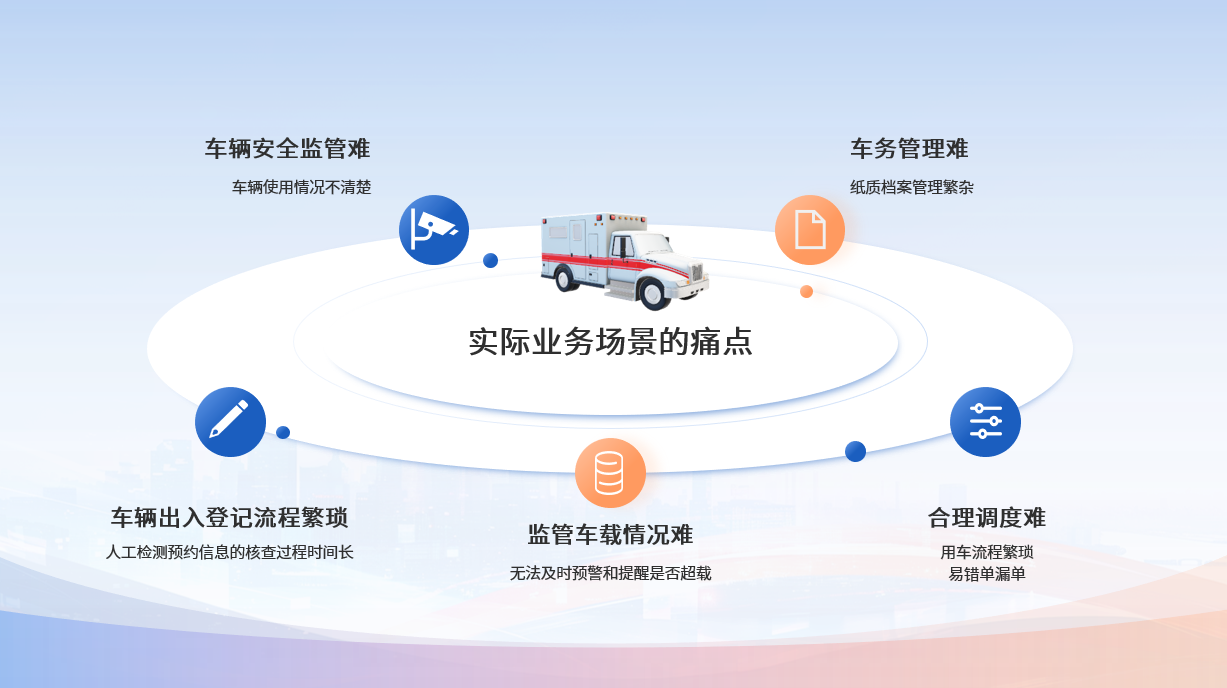
Corporate Goals:
1、To address the issue of numerous form processes and inspection items, which often lead to errors or missing information in form filling, we aim to implement a digitalized vehicle safety management system by embedding the actual vehicle inspection process into a paperless office APP. This will help minimize errors and ensure completeness of information.
2、To tackle the problem of lengthy vehicle entry and exit registration checks, which result in low overall resource circulation efficiency, we propose an automation system that can generate data analysis reports on vehicle appointments, qualifications, and on-board inspections. This will streamline the process and enhance efficiency.
3、Furthermore, to strengthen the management of externally hired vehicles, personnel, and on-board information, we will integrate with the enterprise's own vehicle management platform through data interfaces. This will enable real-time access to summarized information on relevant vehicles, facilitating comprehensive and efficient management.
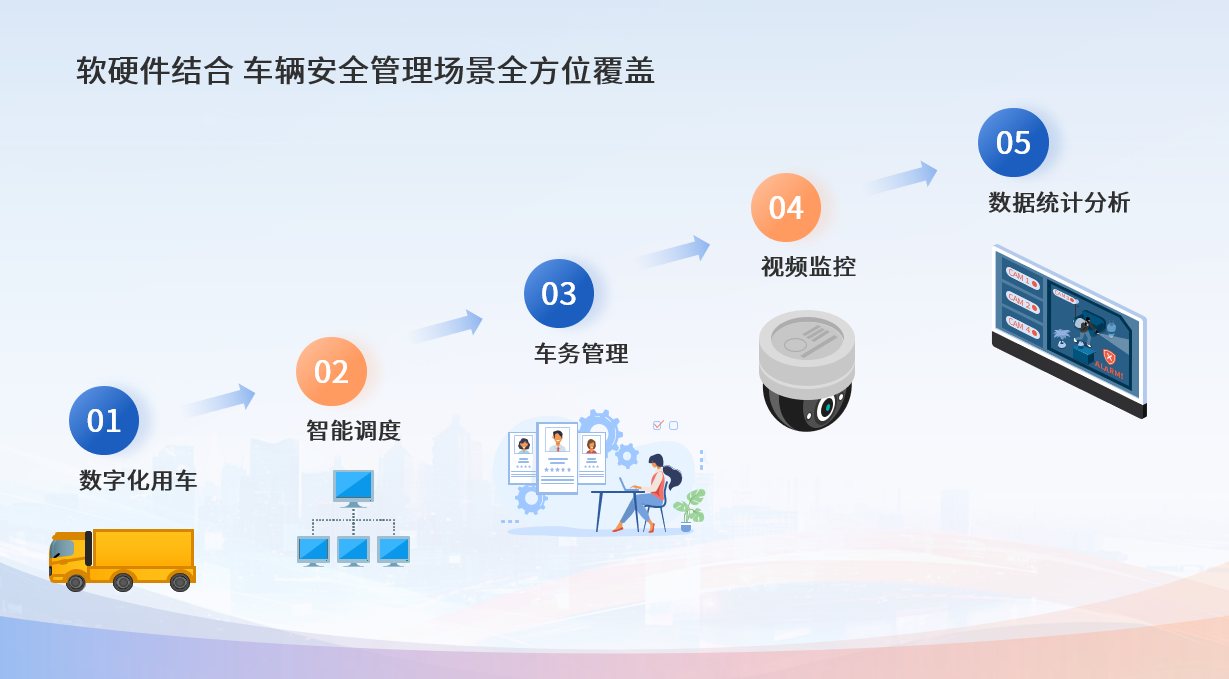
Cooperation Content:
Provide enterprises with a customized, full-lifecycle vehicle safety management solution that integrates hardware and software to comprehensively cover all scenarios.
Cooperation Highlights:
Our customized solution encompasses the entire vehicle safety management chain, including appointment scheduling, intelligent dispatch, vehicle video surveillance, fleet management, statistical analysis reports, and more. It addresses various aspects from hardware selection and software function design to backend data analysis and statistics, as well as real-time status updates such as data analysis, early warning notifications, and more for transport suppliers. This solution enhances corporate vehicle management and improves transportation timeliness, ensuring safety and efficiency throughout the entire process.
Solution:
1、Based on the principles of practicality, stability, and low cost, the vehicle safety inspection software is developed for both iOS and Android platforms, utilizing smartphones and tablets as on-site devices. This software integrates with the enterprise's current reservation system, enabling automatic identification of whether a vehicle has been scheduled.
2、Dispatchers use the application to conduct vehicle safety inspections, confirming each inspection item as合格(qualified) before including the vehicle in shipping arrangements. Simultaneously, the software automatically sends the vehicle safety inspection results back to the reservation system, achieving a paperless operation for vehicle safety checks.
3、The software can automatically compare the scheduled order weight with the actual load to determine if the vehicle is overloaded. It also automatically queries previous inspection items that were not合格(qualified), prioritizing them for the current inspection.
4、In cases where an inspection reveals unqualified items, the software automatically sends a notification email informing of the vehicle's rejection. Additionally, it regularly generates data statistical analysis reports on vehicle management and sends them to designated management accounts.
5、This approach ensures a seamless and efficient process for vehicle safety inspections, streamlining operations, enhancing accuracy, and reducing administrative burdens.
Project Application Value
Enhance Safety: By leveraging software to automatically detect vehicle appointments, load weights, and other critical factors, the system promptly identifies potential safety hazards such as overloading and violations, effectively reducing safety risks during transportation.
Improve Operational Efficiency: Automated detection and data aggregation minimize manual operations, thereby accelerating the efficiency of vehicle entry and exit procedures. Simultaneously, data reports enable both enterprises and suppliers to promptly grasp transportation status, optimizing dispatch and resource allocation.
Strengthen Supply Chain Management: The system comprehensively monitors the transportation status of external suppliers, facilitating efficient management and evaluation of suppliers by enterprises. This promotes continuous improvement within the supply chain. Synchronized reporting feedback to both internal and external suppliers enhances collaboration and transparency, boosting the overall supply chain's synergy and efficiency.
Achieve Fine-grained Management: Through data analysis, enterprises gain a more precise understanding of key indicators like transportation demand and vehicle utilization rates, providing data-driven support for decision-making and realizing fine-grained management. Additionally, it urges supplier vehicles to comply with relevant regulations, such as vehicle weight limits, ensuring more compliant transportation.
Reduce Costs: Efficiency enhancements, reduced manpower, and optimized scheduling contribute to lowering operational costs for enterprises. Furthermore, minimizing safety accident risks averts potential economic losses. Long-term data accumulation assists enterprises in identifying issues, analyzing trends, and providing a basis for continuous improvement.